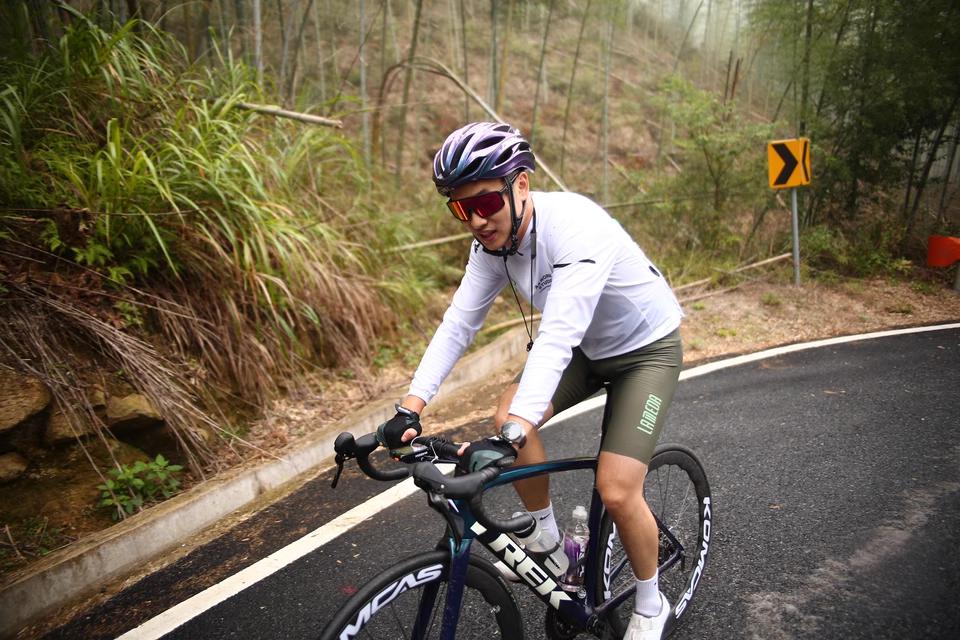
Pursuit of Extreme Lightweight: The Brand Philosophy of Trek and the Common Concept of S-parts Screws
Share
Trek, a world-leading high-end bicycle brand, has always centered its core competitiveness on lightweight design and the application of aerospace-grade materials. This pursuit of ultimate performance aligns perfectly with the R & D concept of S-parts screws - both are committed to enhancing product strength and durability while reducing weight through material innovation and precision craftsmanship.
This article will delve into the brand attributes of Trek and, in combination with the similar ideas in the R & D of S-parts screws, analyze how to optimize product performance through materials science and engineering.
1. Trek's Philosophy of Lightweight Design
Lightweight design is one of the core elements in Trek's brand DNA. Whether it's road bikes, mountain bikes, or urban commuter bikes, Trek is always dedicated to reducing the weight of frames and components to enhance riding efficiency and handling.
1.1 Breakthroughs in Carbon Fiber Technology
Trek's OCLV (Optimum Compaction Low Void) carbon fiber technology represents the top level in the industry. Through high-temperature and high-pressure molding processes, Trek's carbon fiber frames can maintain ultra-high rigidity while weighing over 30% less than traditional aluminum alloy frames.

▲ Trek adopts OCLV carbon fiber technology to achieve extreme lightweight design
1.2 Comparison of Lightweight Properties
Frame Material | Average Weight (g) | Rigidity Index |
---|---|---|
Aluminum Alloy | 1500 - 1800 | 8/10 |
Common Carbon Fiber | 1000 - 1300 | 9/10 |
Trek OCLV Carbon Fiber | 800 - 1000 | 10/10 |
(Data Source: Tests by TREK Official Laboratory)
2. Application of Aerospace Materials
Trek not only focuses on lightweight design but also draws on aerospace technology by using high-end materials such as titanium alloys, magnesium alloys, and 3D-printed titanium metal parts to ensure stable performance of frames in extreme environments.
2.1 Application of Titanium Alloys and Magnesium Alloys
- Titanium Alloys: Used in the welded parts of high-end frames, they are highly corrosion-resistant and possess extremely high strength.
- Magnesium Alloys: Applied to hubs and cranks, they are 20% lighter than aluminum alloys and have higher rigidity.
▲ Trek uses aerospace-grade titanium alloys to enhance frame durability
2.2 Common Points with S-parts Screws
S-parts screws also rely on aerospace materials (such as titanium alloys) to ensure no deformation occurs under extreme torque. For example:
- Aerospace-grade Titanium Screws: Used for connecting high-end bicycle components, they weigh only 50% of steel screws but have comparable strength.
3. The Same R & D Ideas as S-parts Fasteners
Trek's strategies for lightweight design and material optimization highly align with the R & D concept of S-parts screws:
Optimization Direction | Trek Bicycles |
S-parts Fasteners |
---|---|---|
Material Selection | OCLV Carbon Fiber, Titanium Alloy | Titanium Alloy |
Process Optimization | High-pressure Molding, 3D Printing | Cold Forging Process, Precision Turning |
Goals | Lighter, Stronger, More Durable | Higher Torque Resistance, More Lightweight |
4. Conclusion: The Common Pursuit of Ultimate Performance
Trek's success lies in its unremitting exploration of lightweight design and aerospace materials, which is completely in line with the R & D ideas of higher torque resistance and more lightweight design. In the future, with the advancement of materials science, lighter, stronger, and more precise bicycles and fasteners will become possible.
Whether for cyclists or engineers, the pursuit of perfection always shares the same principle - using the most advanced materials to build the most reliable products.